Product Description
Introducing Sinodur®PVDF Resin Polymerized by Suspension for Lithium-Ion Battery - the game-changer in the manufacturing of new energy lithium batteries! With superior product features, endless applications, commendable functions, and remarkable advantages, our PVDF Resin stands out from the competition. Its exceptional chemical resistance, thermal stability, and outstanding mechanical properties make it the ideal choice for battery manufacturing. Unlock the potential of your lithium batteries with Sinodur®PVDF Resin - the ultimate solution for high-performance energy storage!
Product Features
- PVDF Resin Polymerized by Suspension
- Sinodur®PVDF25628, 25630, 2536
- Core extraction without expansion
- High-quality PVDF resin
- Suspension polymerization process
Application of PVDF Resin Polymerized by Suspension
- Chemical processing: PVDF resin can be used in various chemical processing applications due to its excellent chemical resistance.
- Wire and cable insulation: The suspension polymerized PVDF resin provides excellent electrical insulation properties, making it suitable for wire and cable insulation.
- Coatings and paints: The PVDF resin can be used as a binder in high-performance coatings and paints, offering outstanding weatherability and durability.
- Film and membrane production: The suspension polymerized PVDF resin can be used to produce high-quality films and membranes with excellent mechanical and thermal properties.
- Medical applications: PVDF resin is biocompatible and can be used in medical devices, such as catheters and implants, due to its excellent chemical resistance and low toxicity.
-
Sinodur®PVDF25628、25630、2536 are PVDF prepared by suspension method, suitable for lithium batteries in NCM (nickel-cobalt-manganese) system, NCA (nickel-cobalt-aluminum) system, nanocarbon system and lithium iron phosphate system, suitable for high energy density power batteries, high-rate batteries, solid-state batteries and other projects, with superior alkali resistance and stable performance.
Sinodur®PVDF25628

1. Essential characteristics project: This material is a binder for lithium-ion batteries. The product needs to meet the essential characteristics specified in Table 1.
Project
|
Unit
|
Standard
|
Testing method
|
Appearance
|
-- |
White fine particles
|
Visual inspection
|
Molecular weight distribution
|
Da |
100~160W |
GPC |
Density
|
g/cm³ |
1.74~1.78 |
ASTM D792 |
Melting point
|
℃ |
166-174 |
ASTM D3418 |
Water content
|
ug/g |
≤400 |
GB/T 6283 |
NMP solution viscosity (7wt%)
|
mPa.s |
2000~4000 |
Recommended to use 7%-9%
|
2. Recommendations for use
2.1. Suggested dosage of Sinodur® 25628: Ternary NCM523, NCM622 system: 1.2%-1.8%; Ternary NCM811, NCA811 system: 1.5% or more;
LFP system: 2.2%-2.8%, it is recommended to communicate fully before use;
LMO system: 1.4%-1.6%;
LCO system: 1.0%-1.2%.
Note 1: When doped with carbon nanotubes, it is recommended to reduce the above dosage by an additional 0.1% PVDF.
Note 2: PVDF is mainly used to bond positive electrode material particles, and the dosage is mainly determined based on the density and specific surface area of the positive electrode material. If the density of the positive electrode material is reduced or the specific surface area is increased by doping with manganese, cobalt, etc., the proportion of PVDF can be appropriately increased.
2.2. Instructions for use When gluing with the wet method, first quickly mechanically stir for 1.5-2 hours. If the equipment stirring rate is slow or uneven stirring prevents complete dissolution, the stirring time can be increased by 0.5-1 hour, until the PVDF is completely dissolved before entering the pulping stage. The molecular weight of Sinodur® 25628 is ≥110W, and the dissolution rate is slow.
Measures to promote its dissolution can be taken as follows:
1) Increase stirring time appropriately;
2) Increase stirring and dispersing speed appropriately;
3) Add PVDF in batches to dissolve in the stirring kettle;
4) Increase the dissolution temperature in the stirring kettle appropriately.
2.3. Product storage This product is recommended to be stored in dry, ventilated conditions, avoiding light and heat.
2.4. Other For other special usage and storage situations, please communicate promptly with our relevant personnel.
3. Main harmful substance content standards: Compliance with ROHS regulations, harmful substance control standards in REACH; Provide material MSDS; Provide a detection report on resin halogen content; Provide a RoHS detection report, or provide a "No-use RoHS restricted material guarantee certificate"; Provide a REACH detection report, or provide a "No-use REACH restricted material guarantee certificate".
4. Packaging method: Sealed inner plastic bag, sealed packaging in hard cowhide paper square barrel. 20kg/barrel, 500kg/pallet.
5. Product labeling: The Chinese label on the product packaging surface should contain the following information A Product name and specifications B Net weight C Shipping date D Production batch number E Supplier name and trademark F MSDS
6. Transportation and storage: The impact and vibration on the material during handling should be minimized. Avoid exposure to sunlight and fire during transportation and storage. The storage environment should be clean, at room temperature, dry, sealed, while avoiding contamination by chemical vapors and drug particles. In case of special circumstances, such as products being exposed to high humidity for a long time after being opened, it is recommended to dry at 60-80°C before use.
7. Shelf life: The product has a shelf life of 3 years from the date of production.
8. Inspection report: The supplier of this product must provide a product report for each batch of products, including the product name, production batch number (product batch number), production date, quantity, and inspection results.
9. Changes in manufacturing equipment, manufacturing conditions, or processes: In the manufacturing process of the products provided, if there are significant changes in the main raw materials, manufacturing equipment, or manufacturing conditions involved in product production, the second party must obtain the consent of the first party before making any changes.
Sinodur®PVDF25630
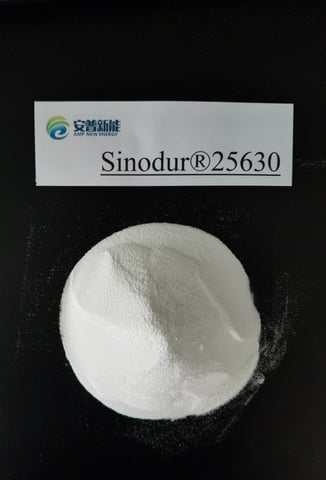
1. Essential characteristics project: This material is a binder for lithium-ion batteries. The product needs to meet the essential characteristics specified in Table 1.
Project
|
Unit
|
Standard
|
Testing method
|
Appearance
|
-- |
White fine particles
|
Visual inspection
|
Molecular Weight Distribution
|
Da |
100~160W |
GPC |
Melting Point
|
℃ |
160-170 |
ASTM D3418 |
Water Content
|
ug/g |
≤400 |
GB/T 6283 |
Viscosity of NMP Solution (7wt%)
|
mPa.s |
2000~6000 |
Recommended for use at 7%-9%
|
2. Usage Recommendations
2.1. Recommended dosage of Sinodur® 25630: This product is mainly suitable for high-nickel ternary systems such as NCM811 and NCA811: above 1.5%; ternary NCM523 and NCM622 systems: 1.2%-1.8%; LFP system: 2.2%-2.8%; LMO system: 1.4%-1.6%; LCO system: 1.0%-1.2%. Note 1: When doped with carbon nanotubes, it is recommended to increase the amount by an additional 0.1% PVDF based on the above dosage.
Note 2: PVDF is mainly used to bond positive electrode material particles. The dosage is mainly determined based on the density and specific surface area of the positive electrode material. If the density of the positive electrode material is reduced or the specific surface area is increased by doping with manganese, cobalt, etc., the proportion of PVDF can be appropriately increased. 2.2. Instructions for Use During wet adhesive mixing, first mechanically stir rapidly for 1-1.5 hours. If the equipment stirring rate is slow or the mixing is uneven and does not completely dissolve, the stirring time can be increased by 0.5-1 hour, until the PVDF is completely dissolved before entering the pulping stage. Sinodur® 25630 has a higher molecular weight, and the following measures can be taken to promote its dissolution: 1) Increase the stirring time appropriately; 2) Add PVDF in batches to the mixing tank for dissolution; 3) Increase the dissolution temperature in the mixing tank to 60°C.
2.3. Product Storage It is recommended to store this product in dry, ventilated conditions, avoiding light and heat.
2.4. Other For other specific usage and storage situations, please communicate with our relevant personnel in a timely manner.
3. Main harmful substance content standards: Compliance with RoHS regulations, REACH harmful substance control standards: Provide material MSDS; Provide testing reports on resin halogen content; Provide RoHS test reports, or provide a "Non-Use of RoHS Restricted Materials Guarantee Certificate"; Provide REACH test reports, or provide a "Non-Use of REACH Restricted Materials Guarantee Certificate".
4. Packaging: Sealed with an inner plastic bag, sealed packaging in a hard cowhide paper square barrel. 20kg/barrel, 500kg/pallet.
5. Product Labeling: The Chinese label on the product packaging should include the following information: A Product name and specifications B Net weight C Shipping date D Production batch number E Supplier name and trademark F MSDS
6. Transportation and Storage: Limit the impact and vibration of materials during handling to a minimum Avoid exposure to sunlight and fire during transportation and storage; The storage environment should be clean, at room temperature, dry, sealed, and avoid contamination by chemical aerosols and drug particles. In special circumstances, such as products being exposed to high humidity for a long time after being unsealed, it is recommended to dry at 60-80°C before use.
7. Shelf Life: The product has a shelf life of 3 years from the date of production.
8. Inspection Report: The supplier of this product must provide a product report for each batch, including the product name, production batch number, production date, quantity, and inspection results.
9. Manufacturing Equipment, Manufacturing Conditions, or Process Changes: In the manufacturing process of the products provided, if there are significant changes in the main raw materials, manufacturing equipment, or manufacturing conditions, the second party must obtain the consent of the first party before making any changes.
Certificate
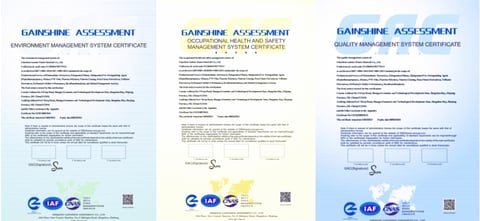