Physical indicators
Test Standards |
Unit |
Sinodur® 2520 |
Sinodur® 2520A |
Exterior condition |
Visual assessment |
- |
White powder |
White powder |
Weight average molecular weight |
GPC* |
Da |
60-100W |
90-110W |
Moisture content |
GB/T 6283 |
ppm |
≤1000 |
≤1000 |
Melting point |
ASTM D3418 |
℃ |
158-166 |
160-166 |
Solution viscosity(7 wt%) |
GB/T 10247 |
mPa.s |
1000-3000 |
3000-5000 |
Product Description
Sinodur®PVDF resin has independent intellectual property rights, and its products coverthe LiBs fields such as LFR, NCM and separator field. With its high bonding, strong alkali resistance and high safety characteristics, it has become the prefened choice of domestic LIBs top enterprises. It has been certified as "international leading" by China Petroleumand Chemical Federation.Typical products list includes Sinodur®PVDF2536 which is used in high- end 3C digital andpower batteries; Sinodur®PVDF25630 used in NCM/NCA with high alkaline resistantence .which is used in high energy density power batteries, other universal products such as Sinodur®PVDF2520/Sinodur®PVDF 2520A and Sinodur®PVDF 25628; battery separator coated highbonding product Sinodur®PVDF 2707, which has full coverage of mainstream cathode systems;all of these products have been approved by batteries customers and work well.
Product Features
- Emulsion Method PVDF Resin
- Suitable for Lithium-Ion Battery Binder
- Sinodur®PVDF2520 and 2520A variants
- Extracts core without expansion
- High-quality binder for Lithium-Ion Batteries
Application of Emulsion Method PVDF Resin for Lithium-Ion Battery Binder
- High-performance binder for Lithium-Ion Battery production
- Specially designed for the Emulsion Method
- Enhances battery performance and stability
- Provides excellent adhesion between electrode materials
- Improves battery cycling efficiency and lifespan
- Ensures uniform coating on electrode materials
- Facilitates rapid ion transfer and high energy density
- Optimizes battery performance in various operating conditions
- Compatible with different Lithium-Ion Battery configurations
- Used in the manufacturing of advanced energy storage solutions
-
Sinodur®PVDF2520、2520A are PVDF prepared by emulsion method, suitable for lithium batteries in the lithium iron phosphate system, applicable to energy storage batteries, high-rate batteries, power tool batteries, small power batteries and other projects, with strong universality and high cost performance.
Sinodur®PVDF2520
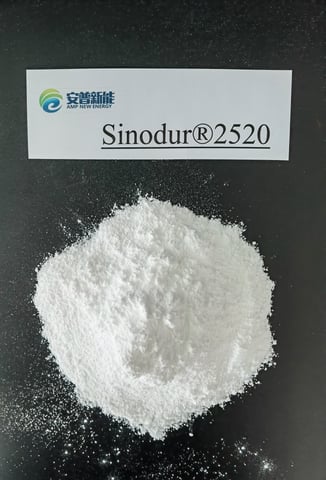
1. Necessary features project: This material is a binder for lithium-ion batteries, with balanced slurry stability and peel strength. The product needs to meet the necessary features specified in Table
Project
|
Unit
|
Standard
|
Test Method
|
Appearance
|
-- |
White Powder
|
Visual Inspection
|
Melting Point
|
℃
|
158~166 |
ASTM D3418 |
Molecular Weight
|
Da |
60~100 W |
GPC, relative to PS
|
Water Content
|
ug/g |
≤400 |
GB/T 6283
|
Volatile Matter
|
% |
≤0.20 |
GB/T 6284
|
NMP Solution Viscosity (7wt%)
|
mPa.s |
1000~3000 |
GB/T 10247
|
2.Instructions for use:
2.1. Recommended dosage of Sinodur® 2520 LFP system: 1.8%-2.5%; Note: PVDF is mainly used to bond positive electrode material particles, and the dosage is mainly determined based on the density and specific surface area of the positive electrode material.
2.2. Instructions for use When using wet bonding, quickly mechanically stir for 3-4 hours. If the equipment stirring rate is slow or the stirring is uneven and cannot completely dissolve, the stirring time can be increased by 0.5-1.0 hours appropriately. After the PVDF is completely dissolved, proceed to the pulping process. When dry pulping, mix the positive electrode material, carbon black, and PVDF for 0.5-1 hour, add solvent kneading for 20-40 minutes, then high-speed stir for 3-4 hours, adjust the slurry viscosity output according to coating requirements.
2.3. Product storage This product is recommended to be stored in dry and ventilated conditions, avoiding light and heat.
2.4. Others For other special usage and storage conditions, please communicate with our relevant personnel in a timely manner.
3. Provide third-party testing standards (mainly harmful substance testing): Comply with ROHS regulations, REACH regulations harmful substance control standards; Provide material MSDS; Provide a resin halogen content detection report; Provide RoHS test report, or provide a "No RoHS restricted material guarantee certificate"; Provide REACH test report, or provide a "No REACH restricted material guarantee certificate".
4. Packaging method: sealed with inner plastic bag, sealed packaging with hard kraft paper square barrel. 20kg/barrel, 500kg/pallet.
5. Product identification: The Chinese markings on the packaging surface should indicate the following: A. Product name and specifications B. Net weight C. Production date D. Batch number E. Supplier name and trademark F. MSDS
6. Transportation and storage: Limit the impact and vibration of materials during handling to a minimum Avoid exposure to sunlight and fire during transportation and storage; Storage environment should be clean, at room temperature, dry, sealed, and avoid contamination by chemical fumes and drug particles. If there are special circumstances, such as products being exposed to high humidity for a long time after opening, it is recommended to dry at 60-80°C before use.
7. Quality shelf life: The shelf life of the product is 3 years from the date of production.
8. Inspection report: The supplier of this product should provide a product report for each batch of products, including the product name, production batch number, production date, quantity, and inspection results.
9. Manufacturing equipment, manufacturing conditions, or process changes: In the manufacturing process of the products provided, if there are major changes in the main raw materials, manufacturing equipment, and manufacturing conditions involved in the production process, Party B should obtain the consent of Party A before making any changes.
Sinodur®PVDF2520A
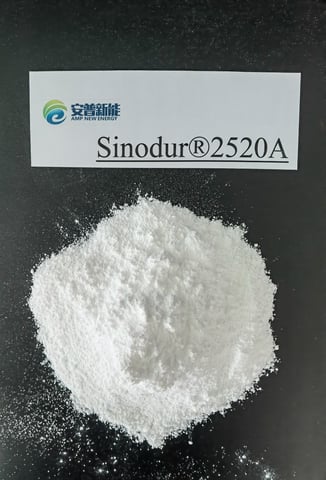
1. Essential Characteristics Project: This material is a binder for lithium-ion batteries, with balanced slurry stability and peel strength. The product needs to meet the essential characteristics specified in Table 1.
Project
|
Unit
|
Standard
|
Testing method
|
Appearance
|
-- |
White powder
|
Visual inspection
|
NMP solution viscosity (7wt%)
|
mPa.s |
3000~5000 |
GB/T 10247 |
Melting point
|
℃ |
160~166 |
ASTM D3418 |
Water content
|
ug/g |
≤400 |
GB/T 6283 |
Volatile matter
|
% |
≤0.20 |
GB/T 6284 |
Particle size D50
|
um |
≤20 |
GB/T 19077-2016 |
Metal element content Fe/Co/Ni/Cu/Zn/Cr/Ca
|
ppm |
|
ICP |
2. Recommendations for Use:
2.1. Recommended Dosage of Sinodur® 2520A LFP System: 1.8%-2.5%; Note: PVDF is mainly used to bond the positive electrode material particles, and the dosage is mainly determined based on the density and specific surface area of the positive electrode material.
2.2. Instructions for Use When wet-gluing, first quickly mechanically stir for 2-3 hours. If the equipment stirring rate is slow or uneven stirring prevents complete dissolution, you can increase the stirring time by 0.5-1.0 hours, until the PVDF is completely dissolved before entering the pulping process. For dry pulping, mix the positive electrode material, carbon black, and PVDF for 0.5-1 hour, add solvent kneading for 20-40 minutes, then high-speed stir for 3-4 hours, adjusting slurry viscosity output according to coating requirements.
2.3. Product Storage It is recommended to store this product in dry, ventilated conditions, avoiding light and heat.
2.4. Others For other special use and storage conditions, please communicate promptly with our relevant personnel.
3. Provide third-party testing standards (mainly hazardous substance testing): Comply with RoHS regulations, REACH regulations on hazardous substance control standards; Provide material MSDS; Provide a testing report on resin halogen content; Provide RoHS testing report, or provide a "Non-Use of RoHS Restricted Materials Guarantee Certificate"; Provide REACH testing report, or provide a "Non-Use of REACH Restricted Materials Guarantee Certificate".
4. Packaging: Sealed plastic bag inside, sealed packaging in a hard cowhide paper square barrel. 20kg/barrel, 500kg/pallet.
5. Product Labeling: The product packaging surface should have Chinese labels indicating the following: A. Product name and specifications B. Net weight C. Production date D. Production batch number E. Supplier name and trademark F. MSDS
6. Transportation and Storage: Limit the impact and vibration of the material during handling to a minimum Avoid exposure to sunlight and fire during transportation and storage; The storage environment should be clean, at room temperature, dry, sealed, and avoid contamination by chemical aerosols and drug particles. If there are special circumstances, such as unpacked products exposed to high humidity for a long time, it is recommended to dry at 60-80°C before use.
7. Shelf Life: The product has a shelf life of 3 years from the date of production.
8. Inspection Report: The supplier of this product must provide a product report for each batch of products, including the product name, production batch number, production date, quantity, and inspection results.
9. Manufacturing Equipment, Manufacturing Conditions, or Process Changes: During the manufacturing process of the products provided, if there are significant changes in the main raw materials, manufacturing equipment, or manufacturing conditions, Party B must obtain the consent of Party A before making any changes.
Certificate
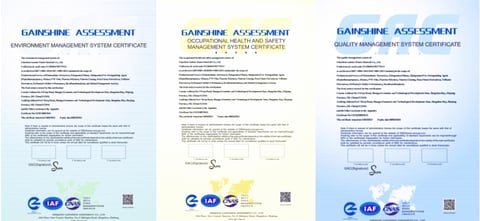